Stainless Steel Hollow Bar and Mesh Stabilizes Failing Slopes at Severn Estuary
The Severn Estuary's frequent slope failures had caused significant disruptions to the Newport to Gloucester rail line, a key route connecting South Wales with North England. DYWIDAG supplied geotechnical materials to stabilize the slopes and prevent future closures and accidents.
Context
The Newport to Gloucester rail line is essential for passenger and freight traffic but has faced repeated disruptions due to slope collapses in the Severn Estuary area. In the winter of 2021, four collapses led to closures, highlighting the need for a permanent solution.
Solution
DYWIDAG developed a solution to stabilize the slopes, some of which reach 37m in height. The solution included installing soil nails, stainless steel mesh, and surface cover. Using stainless steel bars and mesh extended the lifespan from 60 to 120 years, minimizing future maintenance needs. The hollow bar option reduced drilling costs and time on-site, which helped minimize traffic disruptions.
DYWIDAG supplied QTS with the necessary materials, including grade 316 R32-360 stainless steel hollow bars, DYWIDAG EYY drill bits, and stainless steel mesh. Abseil teams and rigs completed the installation, using air flush and secondary grouting for drilling. The project was completed on time and within budget, successfully securing the slopes.
The Severn Estuary's frequent slope failures had caused significant disruptions to the Newport to Gloucester rail line, a key route connecting South Wales with North England. DYWIDAG supplied geotechnical materials to stabilize the slopes and prevent future closures and accidents.
Context
The Newport to Gloucester rail line is essential for passenger and freight traffic but has faced repeated disruptions due to slope collapses in the Severn Estuary area. In the winter of 2021, four collapses led to closures, highlighting the need for a permanent solution.
Solution
DYWIDAG developed a solution to stabilize the slopes, some of which reach 37m in height. The solution included installing soil nails, stainless steel mesh, and surface cover. Using stainless steel bars and mesh extended the lifespan from 60 to 120 years, minimizing future maintenance needs. The hollow bar option reduced drilling costs and time on-site, which helped minimize traffic disruptions.
DYWIDAG supplied QTS with the necessary materials, including grade 316 R32-360 stainless steel hollow bars, DYWIDAG EYY drill bits, and stainless steel mesh. Abseil teams and rigs completed the installation, using air flush and secondary grouting for drilling. The project was completed on time and within budget, successfully securing the slopes.
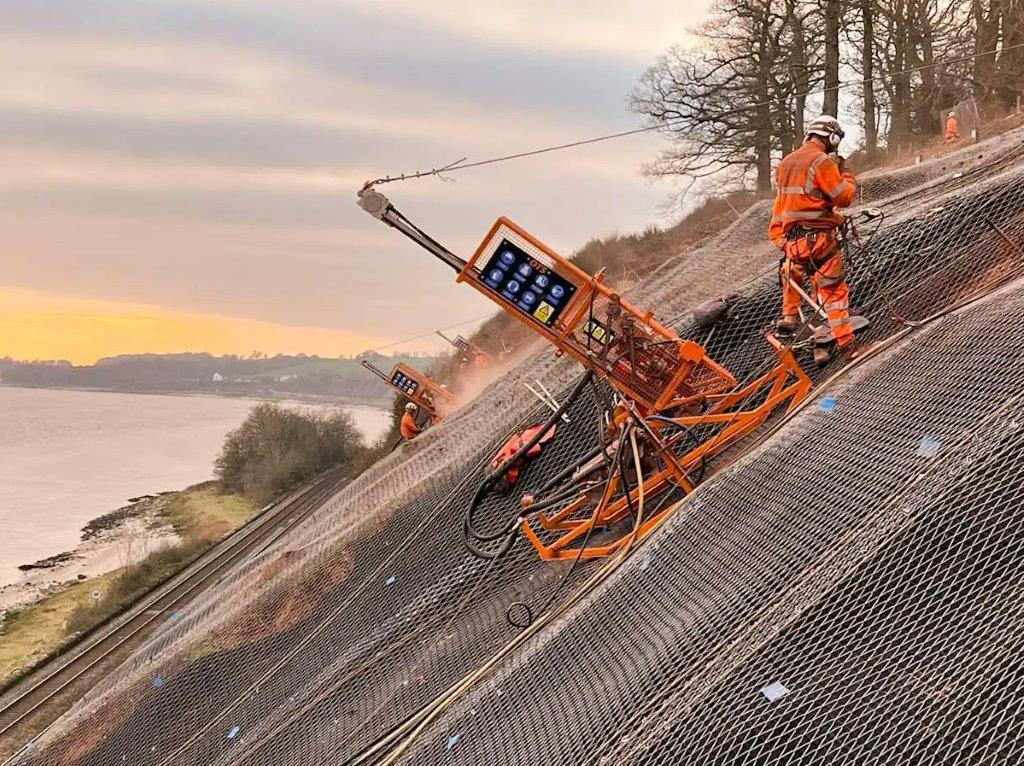
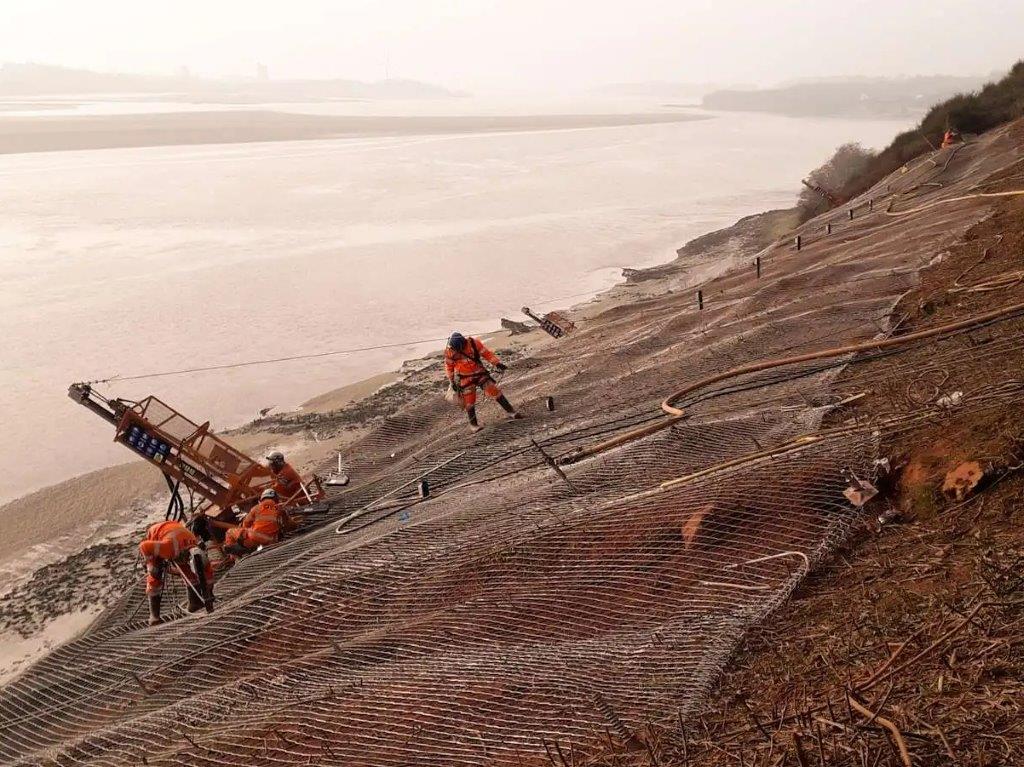
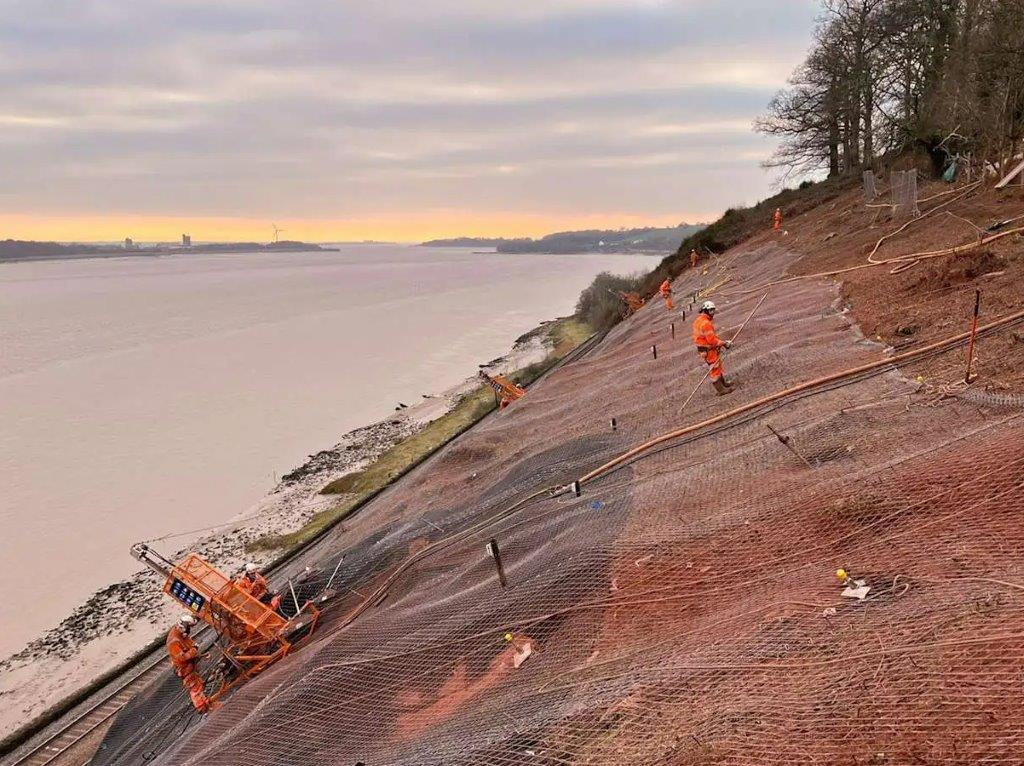
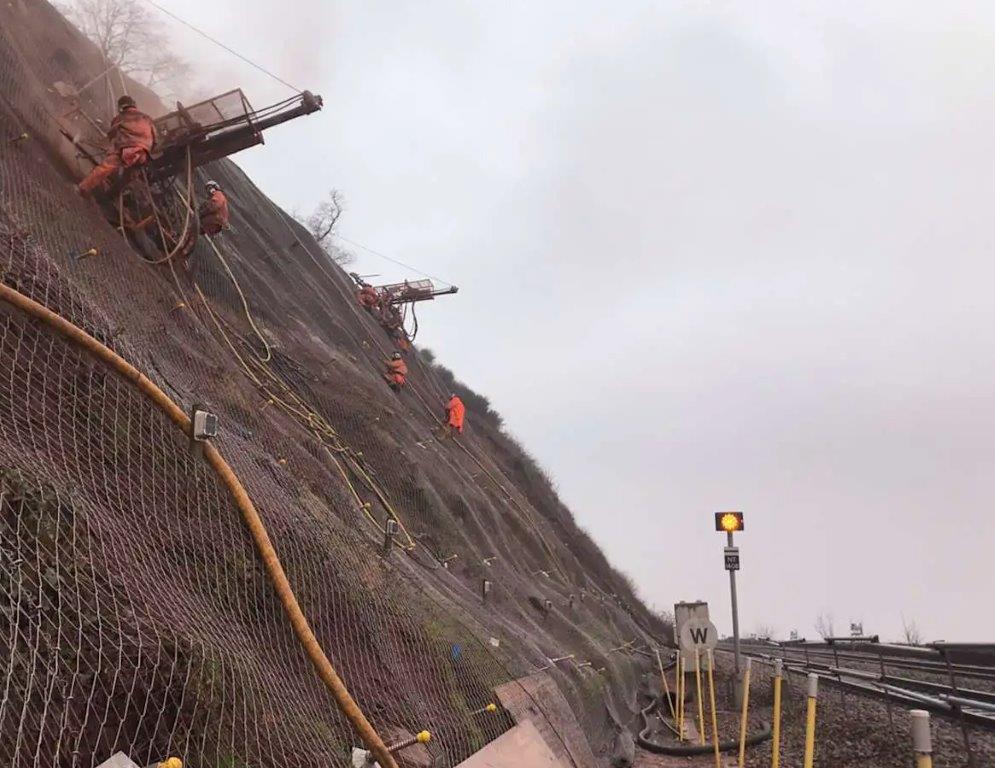